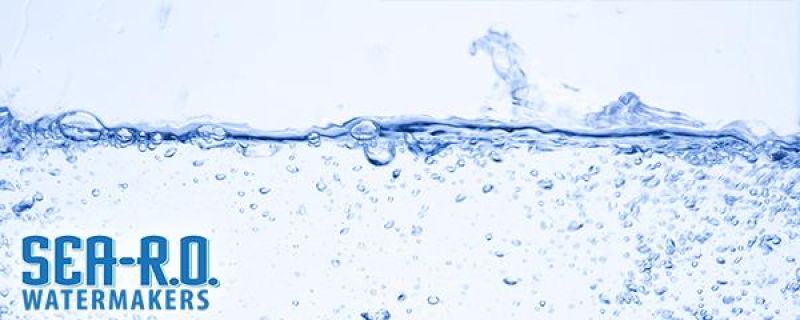
- Watermaker Prefilters
- No comments
Every brand of watermaker requires prefiltration of the sea water prior to the high pressure pump and membranes. This prevents sediments and normal sea life such as plankton and algae from causing any damage to the high pressure pump components which have very close tolerances and also prevents physical fouling of the flow path within the membranes.
While relatively simple in design and function, there are a number of considerations when selecting the prefiltration type which can have a big effect on the overall performance and life of the watermaker.
Prefilter Housing Design
In general, there are two basic filter housing types you will see used in the various systems currently on the market.
1. Sea-R.O. and many others in our industry use what we refer to as conventional or removable sump type housings. For servicing, the entire lower sump portion is unscrewed from the upper head where the inlet and outlet plumbing connections remain attached. The dirty filter cartridge and 100% of any sediment and other accumulations and sump full of water are removed and taken to a sink or drain to pour off the water and dispose of the cartridge. The sump can then be rinsed and wiped clean before inserting the new cartridge and reinstalling. Photo “A†shows an industry standard “Big Blue†housing design used by Sea-R.O. and others.
2. Some other companies use what are essentially hot tub or spa type base mounted filter housings that have a removable lid, normally retained with a retaining ring and to service, the lid is removed and the dirty filter cartridge is lifted out which allows much of the debris to be left behind in the dirty water left in the housing. Photo “B†shows a typical base mount filter. Not only is this a messy procedure to accomplish in the machinery space of a yacht, the worst part is the remaining debris settles to the bottom of the housing and when a new cartridge is inserted, most of the debris is on the outside or discharge side of the filter and when the watermaker is restarted, this debris gets pushed right into the high pressure pump and then on to the membranes. This can cause premature seal failure in some type of high pressure pumps and even catastrophic failure of others along with the detrimental effect on the membranes.
Filter Cartridges
Filter cartridges are made by many different companies all over the world and as long as you have an industry standard filter size, the replacement cartridges should be readily available worldwide. Sea-R.O. and many others use these industry standard filters. Beware of proprietary sized filters such as the base mount type mentioned above, that as well as being a poor design, will also have very limited availability and will cost 5-10 times as much as industry standard filters.
Watermakers require that the filtered water have any sediments larger than 5 microns removed. This is standard on all watermakers and all filter designs will achieve this and can either be done with a single 5 micron rated filter, or duplex filters in series of 20 micron for the larger particles followed by a 5 micron filter for final filtration. Filters should have a pressure gauge on the outlet as a minimum to monitor pressure drop across the filters as a maintenance flag.
The best type of filter to use is a pleated type made of 100% polypropylene. See Photo C. These have the best ability to accumulate the greatest amount of filtered matter and can actually be cleaned and reused. It is not recommended that any cartridges with cellulose content be used as these can break down from lengthy immersion and cause blow by and failure. See photo D.
Sea-R.O. can also design filtration systems for commercial applications and for specific areas where high levels of plankton or algae may be present at certain times of the year, such as the Inside Passage of the Pacific Northwest or the coastal areas of Maine and New England in the summers. Backwashing filters have proven to be very beneficial in these applications.